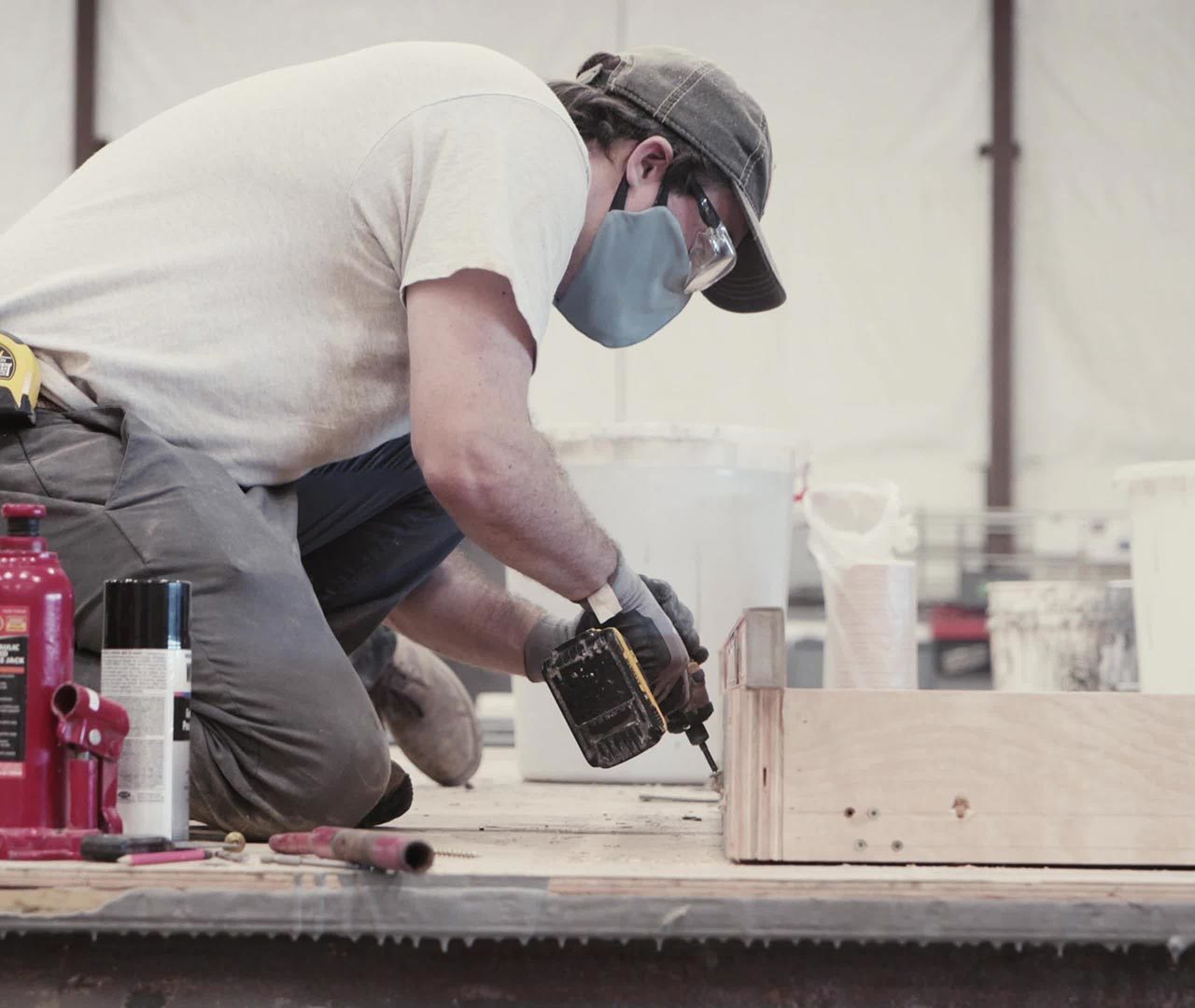
How Are Concrete Formliners Made?
Concrete formliners are an integral part of modern architecture, as they are used to create custom designs on walls and structures that are visually appealing and sturdy enough to withstand the real-world environment.
While they are part of a highly specialized industry and creation process, concrete formliners are used in a variety of everyday applications across the world.
Parking garages, bridges, government buildings, churches, hospitals, sports facilities, and retaining walls of various shapes, sizes, and heights are just a few ways concrete formliners are put to use.
And the versatility of these formliners allows design accents to be added to walls, slab edges, copings, and other aesthetic features.
The results are visually pleasing walls for highways, neighborhoods, parks, and other areas to add character, style, and creativity to an otherwise boring structure.
Creating Concrete Formliner from Plastic or Urethane
Engineers at Scott System start their concrete formliner production process with a design that is cut onto a piece of wood via a CNC machine to create a mold.
The mold is then sprayed with a special coating that allows for easy release when the proprietary urethane and plastic mixtures are poured over it.
This process is completed as many times as necessary for a finished product, then attached together to create a single consistent mold with a wooden frame that surrounds the piece.
The next step to creating the concrete formliner is to pour liquid rubber or plastic in the mold to create the negative image for a specific texture or shape.
In the case of urethane formliners by Scott System, we use elastomeric-urethane, which is a durable and adaptable synthetic compound. This compound is a two-part mixture that must be mixed thoroughly before being poured into the mold.
For plastic formliners, we use acrylonitrile butadiene styrene, or ABS plastic, which is a thermoplastic polymer with no true melting point. Our plastic formliners can be reused about a dozen times depending on the pattern and jobsite conditions.
Once the liquid rubber or plastic is poured into the mold, scrapers are used to spread the liquid evenly as well as to ensure a level surface.
Once cured, the concrete formliners are removed from the mold and laid onto a flat surface until they harden fully.
As a final step, plastic or urethane formliners are cut-to-size as needed, and their edges are processed to remove any fraying or imperfections.
Many of our textures are created to hide the seam lines. Once the concrete is cast, the material looks as though it flows effortlessly without harsh seam lines or a breakup in the texture or pattern.
Begin Your Next Project
Working with Scott System allows teams to work with industry experts to determine if urethane or plastic formliners would be ideal for your project.
Our staff of engineers can help take your project from concept to completion. We can create custom concrete formliners — any size, shape, or texture — to fulfill the needs of your project and our team will work with your team to develop a design that meets your specifications and needs.
Whether it’s concrete formliners for tilt-up installation or precast application, you can learn more about concrete formliners and the capabilities of Scott System by contacting our team today.
Rim Snaps Inlay System: What is it & How Does it Work?
As a leading manufacturer of products for architectural concrete, Scott System has laid the groundwork for concrete textures and architectural solutions for decades. The innovative and time-saving Rim Snaps™ inlay system offered by Scott System creates the versatility needed when casting in-place concrete for clean and functional vertical bridge components like bridge parapets, abutments, and…
Benefits of Extended-Use Urethane & ABS Plastic Concrete Formliners
Different types of extended-use formliners can provide distinct looks on concrete for a wide range of projects. They can also bring an aesthetically pleasing appeal to a variety of finished products. Before beginning your company’s next project, be sure to fully understand the benefits of extended-use concrete formliners offered by Scott System. Each project material…
What Are Brick Snaps®& How Do They Work?
Brick Snap® inlay systems are innovative concrete construction solutions that can speed up and simplify projects, as well as reduce overall costs, while still producing top-quality creative architectural designs with the look and feel of traditional brick. The revolutionary façade system plays an integral role in casting brick into precast or tilt-up concrete, which can…